Laser Marking Systems / Laser Markers
Laser Cleaning
Laser cleaning has been a proven technology for many manufacturers. For years, this process has been helping to remove dust, rust, and imperfections from a variety of surfaces. This cost-effective and efficient solution uses specialised machines, provides many benefits, and can be seen across a number of applications.
Benefits of Laser Cleaning
Industrial laser cleaning is a laser light process that uses ablation to remove coatings or contaminates from a surface. The laser ablation process is a non-contact cleaning laser method that works by focusing a pulsating laser beam on a surface. As the laser pulsates, it eventually releases the top layer from the surface area and leaves behind a clean finish. This process may be focused on a design or over an entire surface area. It is an extremely versatile process that is used across a wide range of industries such as Automotive, Medical, Semiconductor, Electric Vehicle, and Battery Manufacturing. It is a safe way to ensure high quality and consistency across parts. Since laser cleaning can be set to remove foreign material without damaging the integrity of the part itself, foreign material that could damage or affect the efficiency of a part like dirt, oil, paint, rust, oxide, enamel, over-moulded plastic, electrolyte solution, burrs, etc. can all be safely removed through laser cleaning. This makes it a great way to keep costs low and efficiency throughout the manufacturing process very high.
There are a lot of benefits that can be capitalised on from laser cleaning, outside of removing material. Laser cleaning can be used at different steps in the manufacturing process to increase the effectiveness of those processes. For example, laser cleaning a material before welding or applying an adhesive will create a stronger weld/bond. This effect is often called "Anchoring". Also, laser cleaning before applying an adhesive can help to control the pattern, location(s), and uniformity of that adhesive over that area. This is also referred to as "Wettability".
Cleaning contaminates
Rust removal
Oxide removal
Surface preparation
We’re here to provide you with more details.
Reach out today!
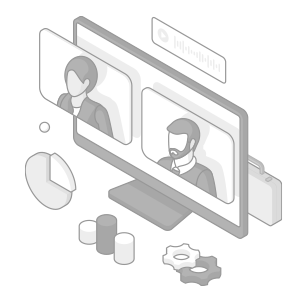
Laser Cleaning vs. Other Technologies
Cleaning can be a vital part of the manufacturing process, and there are many different methods outside of laser cleaning that can achieve this. Other common methods consist of brushing, plasma irradiation, heating systems, and chemical etching. Although there are a lot of options, there is no method of cleaning that is as flexible, versatile, consistent, or hands-off as laser cleaning. In addition, laser cleaning can reliably remove sub-micron levels of material. Therefore, there is far less damage to the surface of a part when laser-cleaned compared to other technologies or methods of cleaning.
Unprocessed
Processed
Anchoring
Laser cleaning before other steps in the manufacturing process can lead to more efficient and effective final products. Laser cleaning before applying an adhesive or welding can lead to a significantly stronger bond/weld between parts. This is due to the laser cleaning process creating more surface area and texture for the adhesive or weld to hold onto. If a stronger bond is not necessary, laser cleaning the surface will allow the same bond or weld strength to be achievable in less time, thus speeding up the manufacturing process. This effect is often called "anchoring".
Unprocessed
Processed
Wettability
When applying adhesive or a different liquid to a surface, it is often difficult to control the distribution of that liquid due to the bonding in the liquid itself. When a surface is laser-cleaned before the application, it allows the adhesive to have a more even distribution across the laser-cleaned surface. This helps avoid any pooling or inconsistencies. Another advantage of laser cleaning beforehand is that the laser can easily clean the surface with any shape or desired pattern, which can lead to a stronger bond and the potential for less adhesive on each workpiece. This effect is often called "wettability".
Pre-processing
Post-processing
Deburring
A burr is a small unwanted piece of material or raised edge that is still attached to the part after some portion of the fabrication process. Burrs can be stress concentrators that shorten the expected life of a part or increase the risk of corrosion. In situations where they are found on current collectors or other electrical pieces, they can create concentrated points for electrical charge, leading to a risk of static discharge. Laser cleaning gives the ability to very quickly and consistently remove these burrs. Therefore, adding laser cleaning into this manufacturing process removes the risk provided by the burrs and reduces potential scrap or defective products.
Pre-processing
Post-processing
Discover more about this product.
Click here to book your demo.
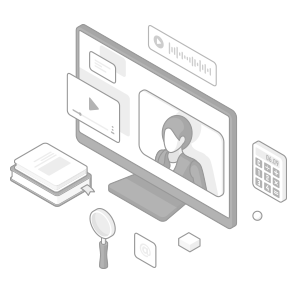
Laser Cleaning Machines
3-Axis Hybrid Laser Marker MD-X Series
The 3-Axis Hybrid Laser Marker MD-X Series is a combination of a fibre laser and a YVO4 laser. It combines the two strengths of each laser. Fibre lasers are designed for long service life and high output. YVO4 lasers are designed for high quality and depth of focus. Together, these lasers create the MD-X with high peak power and a short pulse laser.
The high peak power and short pulse laser result in minimal heat damage while still having a powerful laser. Since laser cleaning often requires very quick cycle times while keeping damage to the surface at a minimum, the MD-X's Hybrid technology provides a serious advantage. With autofocus and built-in cameras, the MD-X can clean surfaces while assuring it is in focus and hitting the correct surface, even in the case of shifted or unfixed parts.
Get detailed information on our products by downloading our catalogue.
View Catalogue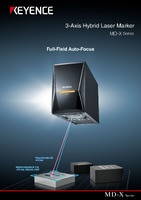
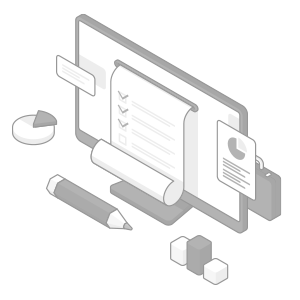
Laser Cleaning Applications
Laser cleaning technology has found significant applications in both the automotive and aerospace industries for precision, environmental friendliness, and efficiency.
In the automotive industry, laser cleaning plays an important role in manufacturing processes. It also aids in the maintenance and restoration of vehicles and their components. During manufacturing, laser cleaning ensures that surfaces are pristine and free from contaminants before coatings or adhesives are applied. This enhances the quality and durability of the final product.
In vehicle maintenance and restoration, laser cleaning is used to remove rust, paint, and corrosion from automotive parts. This includes engine components, brake calipers, and chassis. The process is non-abrasive and leaves the underlying material intact, preserving the structural integrity of the components. Laser cleaning not only improves the appearance of used parts but also extends their lifespan, contributing to cost savings and sustainability efforts.
In the aerospace sector, where precision and safety are non-negotiable, laser cleaning is very useful. It is used to remove dirt, corrosion, and paint from critical parts such as turbine blades, landing gear, and fuselage surfaces. By effectively eliminating contaminants, laser cleaning helps prevent premature wear and corrosion-related failures.
In addition, laser cleaning is essential during the manufacturing of aerospace components. This proven process results in enhanced product quality and longevity. It also reduces the need for frequent replacements and expensive maintenance.
Besides these industries, others are also finding useful applications for laser cleaning systems. As laser cleaning machines continue to advance, we expect to see more use cases evolve.
We’re here to provide you with more details.
Reach out today!
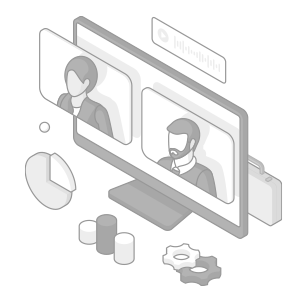
Industry Benefits from Laser Cleaning
Aerospace
The aerospace industry frequently uses cleaning processes—such as removing coating every five years from airplanes for inspection and upgrading purposes. Industrial laser cleaning benefits the aerospace industry because of how non-damaging the process is. The coating is only removed for maintenance reasons, so utilising a non-invasive technique like laser cleaning keeps the airplane components intact.
Automotive
The automobile industry commonly uses cleaning techniques like paint removal to create contrast on vehicle switches. The contrast is for identifying designs on the vehicle switch, so laser cleaning is optimal for this process. Industrial laser cleaning uses a thin and focused beam that can create precise designs without ruining the whole surface area.
We’re here to provide you with more details.
Reach out today!
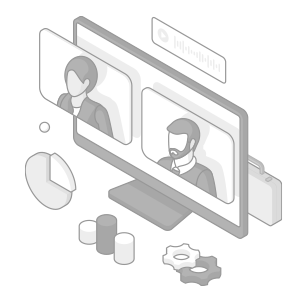
Avoid Damaging the Substrate
The main benefit of laser cleaning is that it does not damage the substrate of a part or component. Instead, it only removes the top layer.
Alternative cleaning options like chemical etching or shot blasting can damage the substrate because of their forceful and un-precise processes. When cleaning, there is just enough force to remove the top layer without threatening the integrity of the substrate.
Discover more about this product.
Click here to book your demo.
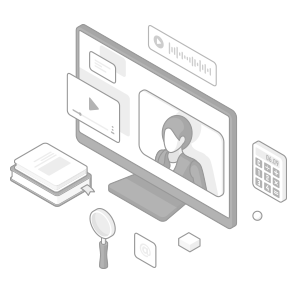
Safety With Laser Cleaning
Laser cleaning is a generally safe process, especially compared to its competitors. Industrial laser cleaning requires no dangerous toxins or materials that could cause sickness or bodily injury.
Cleaning options like chemical etching use toxins that can burn skin or cause sickness and shot blasting can also be dangerous to the skin and body. These cleaning processes both require PPE equipment and strict safety protocols.
We’re here to provide you with more details.
Reach out today!
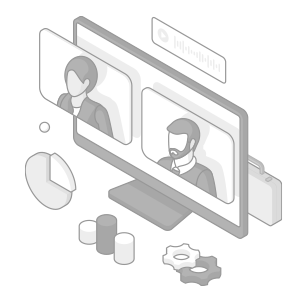
Decrease Environmental Footprint With Laser Cleaning
As climate change becomes a more pressing issue, the environmental impact of manufacturing emissions and toxins is a growing concern. Industrial laser cleaning is a green option for cleaning parts and components. Using an environmentally clean laser machine does not produce any toxic waste that seeps into the air or needs to be disposed of into the environment.
The environmental impact that industrial laser cleaning achieves is the opposite of sandblasting and chemical etching. These processes litter the air with toxins and produce excessive amounts of waste that cycle back into the environment.
We’re here to provide you with more details.
Reach out today!
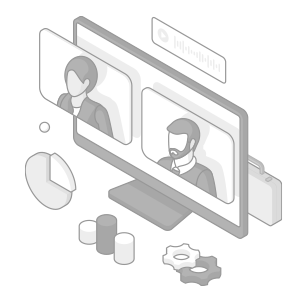
Decrease Costs for Maintenance With Laser Cleaning
Since industrial laser cleaning does not require extra materials like accessories or chemicals, it decreases maintenance costs for manufacturing. In fact, using KEYENCE's best laser cleaning machine, the Hybrid Laser Marker MD-X, includes the opportunity for you to get quick on-site and over-the-phone maintenance support.
As you can see, laser cleaning has become an essential step for a multitude of industries in the manufacturing realm. With the implementation of laser cleaning in the rapidly expanding electric vehicles and the semiconductor industries, more and more industries are finding uses for laser cleaning in their process to more efficiently and effectively manufacture their parts.
Get detailed information on our products by downloading our catalogue.
View Catalogue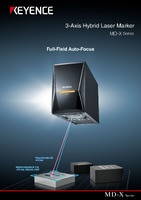
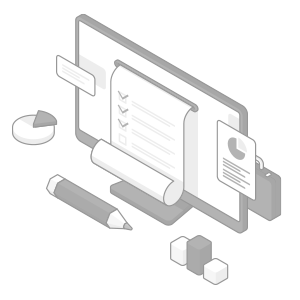