Laser Marking Systems / Laser Markers
Laser Oxide Removal
Oxidation is the naturally occurring surface change created by metal’s interaction with oxygen. Oxidised metal signifies the first step in corrosion and is not aesthetically pleasing. Additionally, the oxidised surface is incompatible with other processing methods like welding, moulding, and extruding because it is not a clean and workable surface area.
Although it is not super harmful, it is not preferred and often requires removal. Fortunately, there is a solution. Conducting laser oxide removal is a precise and efficient method for combatting the inconvenience of oxidation. In the following, we will discuss the ins and outs of KEYENCE’s laser oxide removal methods.
Laser Oxide Removal Process
Laser machines use ablation for effective metal and aluminium oxide removal. Ablation is a specialised laser oxide removal cleaning technique that utilises high peak power and short-frequency pulses to evaporate oxide. Once the ablation evaporates the oxide, the underneath surface has a clean finish ready for more processing.
Discover more about this product.
Click here to book your demo.
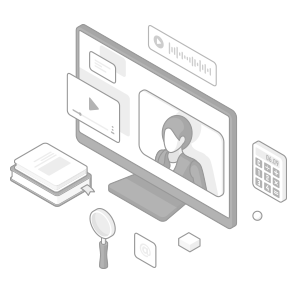
KEYENCE’s Laser Oxide Removal Machine Features
High Outputs
KEYENCE's MD-X Series Hybrid Laser marker has proven to be an optimal system for laser ablation due to its high output power and short pulse width, resulting in superior absorption.
- 3 Axis Hybrid Laser Marker MD-X Series
- Combining the high output power of a Fibre laser system with the extremely high peak power of a YVO4 system, KEYENCE's MD-X Series offers incredible flexibility no matter the ablation requirements.
3-Axis Control
The 3-Axis control built into each of KEYENCE's laser machines allows for a variable focal point. This means common limitations of fixed distance lasers including 3 multiple focal heights, large trays of parts, and 3 Dimensional shapes, can be easily handled by KEYENCE lasers with no distortion.
Autofocus
The autofocus feature of the hybrid laser marker works with the 3-axis control to accentuate the flexible benefits even more. Not only does the 3-axis control work to ablate even hard to reach target points, the autofocus assists with positioning.
The benefit of smart positioning, known as KEYENCE’s autofocus feature, is that positional and focal deviation of the target is tracked for maximum efficiency and precision. It removes the tedious placement process. And it prevents accidental processing in the wrong area. Targeted processing is crucial for aluminium since it is sensitive, so the ablation process has to be extra careful only to conduct oxide removal.
Get detailed information on our products by downloading our catalogue.
View Catalogue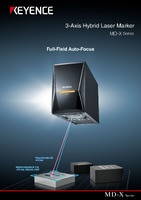
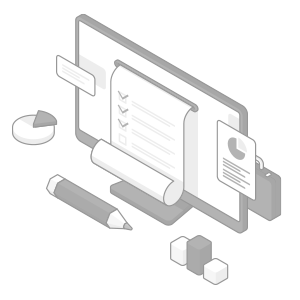
KEYENCE Oxide Removal Solutions
KEYENCE is an industry leader in specialised laser technology for processing applications. Removing oxide with a laser is an efficient, clean, and precise method that makes your metal ready for more processing, from welding to shaping. From small metal parts covered in oxide to significant components with hidden oxidation, KEYENCE lasers can tackle it all.
Ready to start your laser oxide removal project? Contact KEYENCE today! Our team will get back to you immediately with advice about a suitable machine for you and how to demo our products.
We’re here to provide you with more details.
Reach out today!
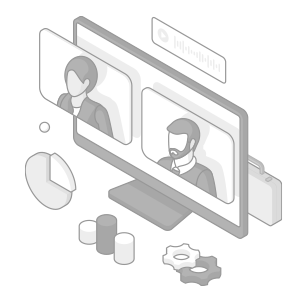