Laser Marking Systems / Laser Markers
Laser Marking in the Medical Industry
-
Tags:
- Laser Annealing , Metal , Plastic
Medical devices are crucial tools used to diagnose, prevent, or treat various conditions or illnesses. Since these tools are life-altering, they follow a strict regulatory guidline to ensure saftey and quality, which require permanent traceability marks that can be read by humans and machines. Since the majority of medical instuments are small and designed to be used repeatedly after undergoing a disinfection or sterilization process, permanent and legible traceability is difficult. Labels or ink cannot be used in these cases, but laser marking provides the ideal solution for this direct part marking.
Direct Part Marking in the Medical Industry
Medical laser device marking refers to the process of engraving or permanently marking medical devices with identifying text and/or images. This can include serial numbers, barcodes, logos, and other unique device identifying marks. Laser medical device marking is an alternative to traditional medical device markings such as printing or stamping.
These device markers offer many benefits over traditional methods including faster marking speed, the ability to mark small or difficult to reach areas, and cleaner and more consistent marks. Additionally, laser marking medical devices provide high resolution marks, utmost accuracy, flexibility, and overall operational efficiency.
Needle hubs
Catheter connectors
Medical tubes
Instrument covers
Small steel objects
Catheter wire
Drill bits
Medical bolts
Medical device laser marking is an essential part of the medical device manufacturing process. This process helps to ensure that each device is accurately and precisely marked. For example, if there is ever a recall of a medical device, the identifying marks can be used to quickly and easily identify which devices are affected. This process is also important for traceability purposes and FDA compliance, as previously mentioned. There are many different types of medical devices that can be marked with lasers, including parts such as stents, dental implants, hip replacements, pacemakers, catheters, and surgical tools as seen above.
Laser medical marking is a safe, permanent, compliant, and efficient way to mark medical devices. At KEYENCE, we offer high quality laser markers that can meet the needs of any medical application. Our laser medical device markers are backed by our extensive knowledge and experience in the field of lasers and laser applications.
We’re here to provide you with more details.
Reach out today!
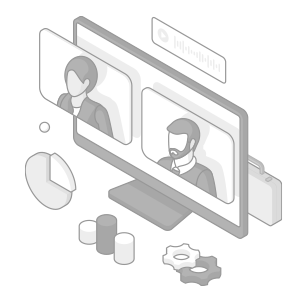
Reduced Lead Time, Manufacturing Costs, and Environmental Impact
Software Setup
- Reduce manufacturing costs by creating custom programs that adjust for design and part changes.
- Laser marking creates permanent, high-contrast marks without the use of ink.
- Marking can be performed during the manufacturing process, which eliminates the need for extra machinery and additional processing time.
Discover more about this product.
Click here to book your demo.
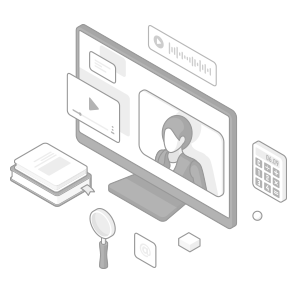
Complex Part Marking
3-Axis Marking
With KEYENCE's Z-MAP Creator software, 3D CAD data (STL format) can be imported directly into the Marking Builder software. The data can then be used as a foundation for three-dimensional marking. Characters and logos can easily be marked on even the most complex shapes with just the touch of a button. Because of its ease-of-use and high functionality, Z-MAP Creator has become an essential tool in surgical device manufacturing.
Discover more about this product.
Click here to book your demo.
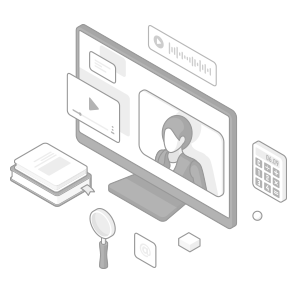
Direct Marking on Steel Medical Instruments
High-Speed, Precise Marking
Laser markers are used to create identifying marks (like 2D codes) on surgical equipment. These marks are highly visible, don't wear off and can't be erased by chemicals (which is a common problem with pad printers).
Laser Marking Part/Lot Numbers on Medical Tube Connectors
Laser markers can mark both metals and plastics, and they're commonly used to create identifying marks on polycarbonate medical tubing. This identification process is typically accomplished with labels, but they are expensive, take time to produce and run the risk of falling off or being removed. Laser marking eliminates those risks and the costs associated with each.
Discover more about this product.
Click here to book your demo.
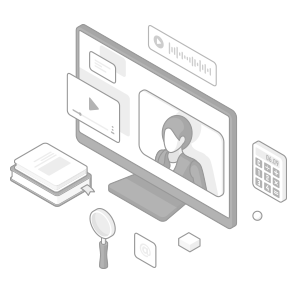
Direct Marking on Plastic & Synthetic Materials
Permanent, Sharp Markings
Laser marking intravenous bags creates a permanent, easy-to-read mark. Date codes and serial numbers are common marking examples. Ink printing (which is a common marking alternative) easily wears off and heat stamping is not clearly legible. Replacing either system with a laser solves both issues and eliminates the costs associated with maintenance and consumables.
Laser Processing on the Surface of Catheters
Laser markers can also be used on catheters and hypodermic needles. Cut locations and dwelling positions can be marked in the fluoride coating. Ink systems are commonly used to create these marks, but there's a risk the ink will contaminate the product. Laser markers remove this risk since no chemicals are used in the marking process.
Medical laser marking is mandated and regulated by the FDA in the United States and the corresponding medical regulatory bodies in other countries. The FDA has established guidelines for unique device identifiers, or UDIs, which must be followed by medical device manufacturers and labelers or markers. These guidelines include specific requirements for various medical device types, such as Class 1, Class 2, or Class 3.
As the FDA site states:
“The FDA established the unique device identification system to adequately identify medical devices sold in the United States from manufacturing through distribution to patient use.
When fully implemented, the label of most devices will include a unique device identifier (UDI) in human- and machine-readable form, which will ultimately improve patient safety, modernize device postmarket surveillance, and facilitate medical device innovation (source).”
These identifiers consist of the device identifier, which is the mandatory mark to identify the device’s version or model. Next is the production identifier, which may include a lot or batch number, serial number, expiration date, and manufacturing date. In order to implement these UDI’s, an accurate laser marking machine that is customised for these specific medical-related requirements must be used.
Following the FDA guidelines is essential to ensure patient safety and avoid unnecessary regulatory issues.
We’re here to provide you with more details.
Reach out today!
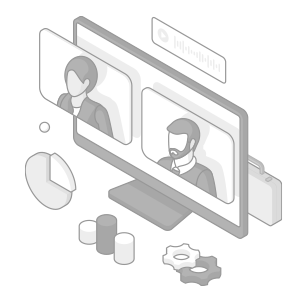
FAQs about Laser Marking in the Medical Industry
What’s the best laser engraving machine for medical technology?
UV laser technology was developed with the medical industry in mind. "Cold Marking" capabilities due to improved absorption from the shortened wavelength appeals to many applications in the medical industry due to a decreased HAZ (Heat Affected Zone).
How are implants and surgical instruments marked with the laser machine?
Implants and Surgical instruments are marked in a variety of ways. The end goal with each marking is implementation of tracking and traceability as well as unique device identification (UDI). 2D data matrix/QR Codes, serialised information, and regulatory logos can all be added via laser marking.
Does laser marking wear off?
Lasers interact directly with the surface of the material to create a permanent mark. Laser marks will not wear off without fully removing the layers of material that interacted with the laser.
What are the different types of medical lasers?
Lasers have nearly endless application potential in the medical industry. Commonly known procedures such as eye surgery, hair, and tattoo removal utilise laser technology. The laser systems offered by KEYENCE are targeted for production companies in the medical industry to tackle the growing demand for unique device identification (UDI) and selective material processing.
What are medical lasers used for?
Unique Device Identification (UDI) is a common requirement for medical devices. Lasers are the optimal technology for this as they can provide permanent marks without damaging or compromising the device.
What is the minimum font size that a laser can mark?
The minimum achievable font size is dependent on the laser's beam spot and selected based on the material you intend to mark. Under perfect conditions text sizes as small as 100um are possible.